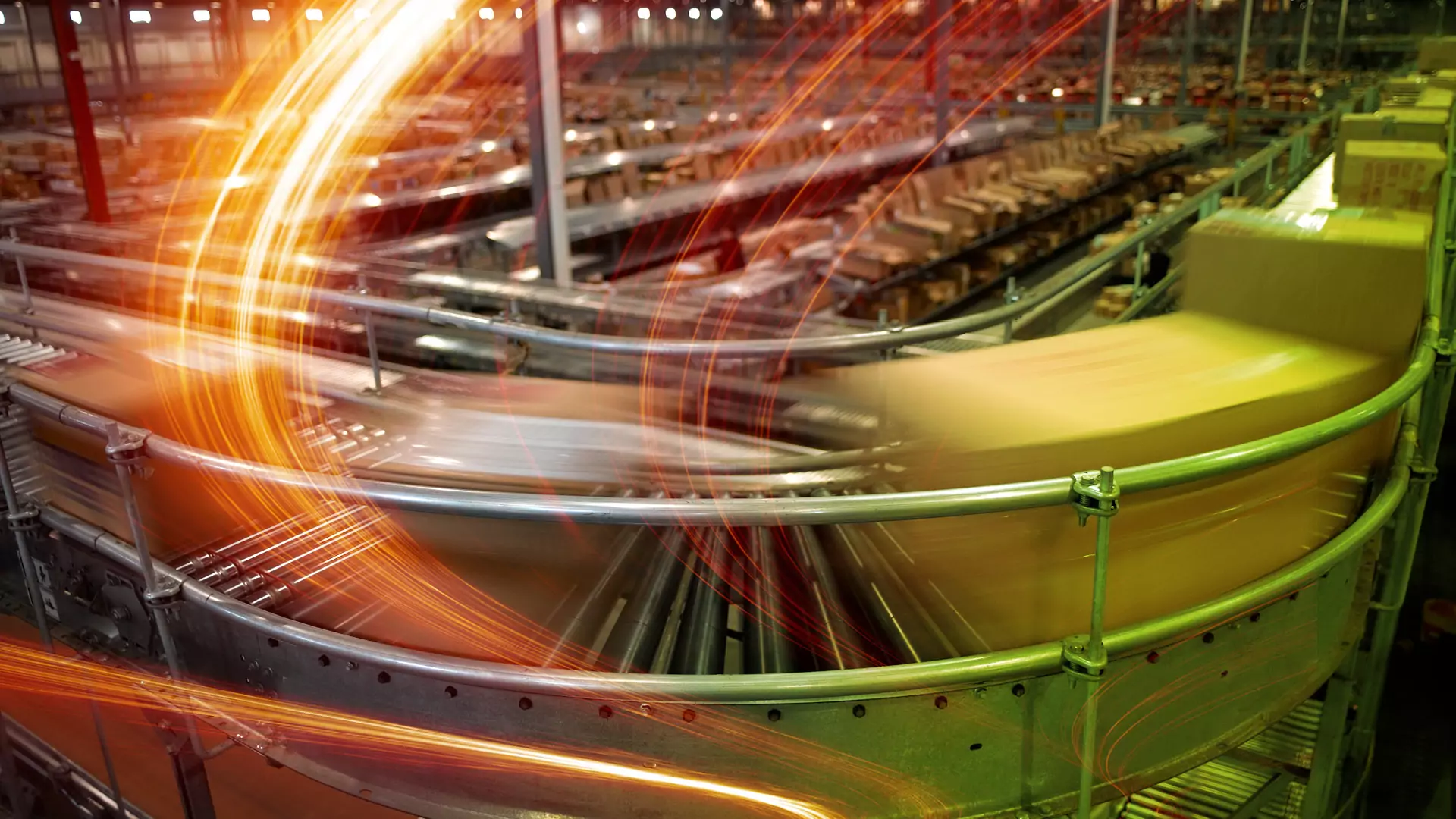
Vaccine Logistics: Modular Coolers fit all Vaccines
The more vaccines are licensed, the more complex the requirements for vaccine logistics. This is because each vaccine has different temperature and thus transport and storage conditions. This makes it all the more useful to have adaptable packaging that fits all transport volumes, all temperature corridors, and thus all vaccines. The modular refrigerated packaging system from the Mannheim-based company eutecma, which is unique on the market, has been used thousands of times during the pandemic – at vaccination and distribution centers as well as by government agencies and mobile vaccination teams.
The so-called Protect system boxes and Icecatch cooling elements that make up the eutecma packaging system have several special features. Depending on how many Styrofoam rings are placed on top of each other, the capacity of the high-tech boxes changes. The largest box, the Protect XL Box, can thus be adjusted to five heights and can hold 335, 648, 961, 1,275 or 1,588 liters of cargo. The advantage: instead of shipping a box only half-full in a truck or on a plane, only the payload that is de facto required is utilized. The universal Icecatch cooling bricks, in turn, are available for all temperature spectrums: Frozen (<-20 °C), Cool (+2 °C to +8 °C) and Ambient (+15 °C to +25 °C). Firmly anchored in the side walls of the ProtectBoxes, they deliver energy evenly and keep the sensitive vaccines in the correct temperature corridor for up to 120 hours. Deep-frozen transports at <-70 °C can also be guaranteed by eutecma thanks to dry ice.
Optimal for fluctuating freight numbers and staggered delivery quantities
Boxes and cooling elements that fit all vaccines have both practical and economic advantages. After all, if personnel – regardless of which vaccine has to be shipped – only have to handle one box and the matching universal cooling elements instead of several, process errors in the packing process are virtually eliminated. The economic benefits of modular vaccine boxes result from significant weight and cost savings, which are particularly noticeable in air freight. This is because, as a result of the Corona pandemic, many planes are still grounded on many routes, resulting in a shortage of air freight capacity worldwide – and that means higher freight prices. “Manufacturers and shippers should take care to make the pack-out – the filling of the boxes – as efficient as possible so as not to waste space. This is exactly what our modular packaging system makes possible,” says eutecma Managing Director Florian Zeilfelder.
But also for truck transport on the ground, the eutecma packaging system plug-in system proves its advantages. Because not every box makes sense always and everywhere. If, for example, only small quantities of vaccine are available, the height of the side walls of the system boxes can be reduced by the appropriate number of rings in a few simple steps, thus reducing the packing volume. If more vaccine doses have to be moved ad hoc, the maximum payload is exhausted by the maximum number of rings. Ergo: The modular system adapts to different delivery phases and is particularly well suited for fluctuating freight numbers.
Quickly invested at the start of the pandemic
The challenges of the Corona pandemic to the packaging industry were recognized early by eutecma. “As early as spring 2020, many of our customers ramped up their stocks of pharmaceutical refrigerated packaging for safety reasons. We quickly adapted to this development and made additional investments,” says co-managing director Markus Baumgärtner. The 50 employees at the Mannheim port are working at full capacity, the warehouses are well stocked, and production is running in multiple shifts. Several million Icecatch Solid cooling elements and the corresponding PROTECT system packaging (insulating boxes) in various sizes leave the factory halls in Mannheim Harbor every year. Since its foundation, the specialist for temperature-controlled goods has recorded growth rates of 20 percent per year.
temperature ranges and freight volumes without any problems comes from
eutecma. No other box manufacturer offers this. (Image source: eutecma)